Tailored Salesforce Experience Cloud for enhanced ERP of a technical textiles manufacturer
How we implemented a customized solution for a UK technical textiles manufacturer, automating production tracking, integrating machinery and accounting systems, and enhancing inventory management, which resulted in reduced waste and streamlined operations.
Client & product
Our customer is a UK-based technical textiles manufacturer founded back in 1954. The company has successfully established a global customer base spanning across 50 countries by unwaveringly prioritizing excellence. Through their steadfast commitment to quality, adhering to ISO 9001 quality standards, their exceptional technical knowledge, and integrated approach, the manufacturer has positioned itself as a leader in the industry.
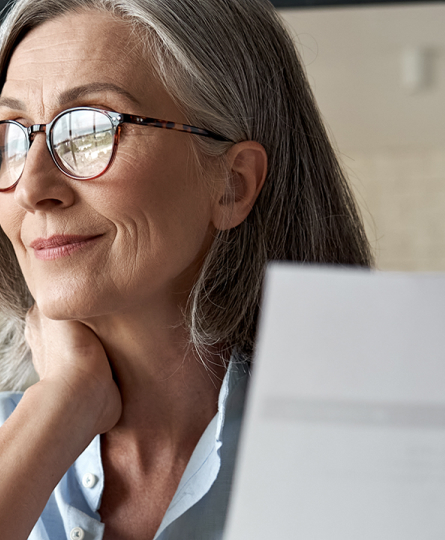
Business challenge
The client has chosen Salesforce to help them build a unified ERP system that, among other things, streamlined manufacturing and production processes. Working with technical textiles, tracking them, and calculating the exact amount of textile produced by each machine used to require a lot of manual support, and often caused unnecessary waste and unpredictable expenses, leading to poor operational efficiency.
To help the manufacturer overcome this issue, Noltic implemented Salesforce to automate manufacturing processes, track the amount of textile in stock, eliminate the need of manual input and generally streamline the operations.
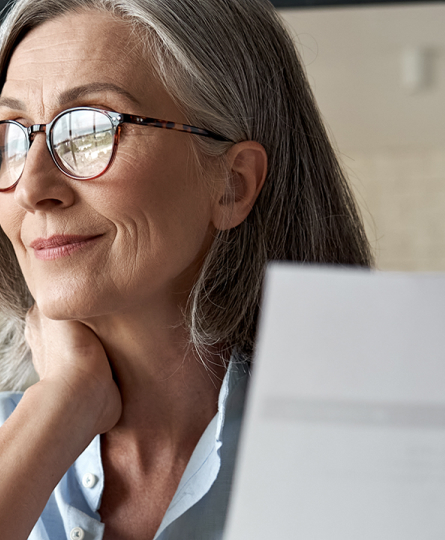
Partner with Noltic to automate production, integrate systems, and optimize inventory management with custom Salesforce solutions.
Facing Salesforce challenges?
Need a reliable partner?
Results achieved
- Built a unified, full-cycle ERP system from scratch;
- Enabled efficient and streamlined inventory management processes;
- Reduced thread waste by developing a Salesforce-based application that translated into lowered costs of production.
Business impact
Our solutions
- Developed a sophisticated software that accurately calculates the fabric production from the manufacturer's machinery;
- Created an application that seamlessly integrates with on-premise production machinery, providing insights into the fabric production volumes;
- Implemented a custom integration between Salesforce and the accounting system Sage 200, resulting in a seamless and synchronized flow of data. This integration empowered the client to effortlessly track and monitor individual client balances, enhancing financial visibility;
- Created and implemented an integrated document generation and management system that helped optimize document workflows and improve overall efficiency in business operations;
- Utilized Gimbal Barcode Scanner for efficient inventory accounting.
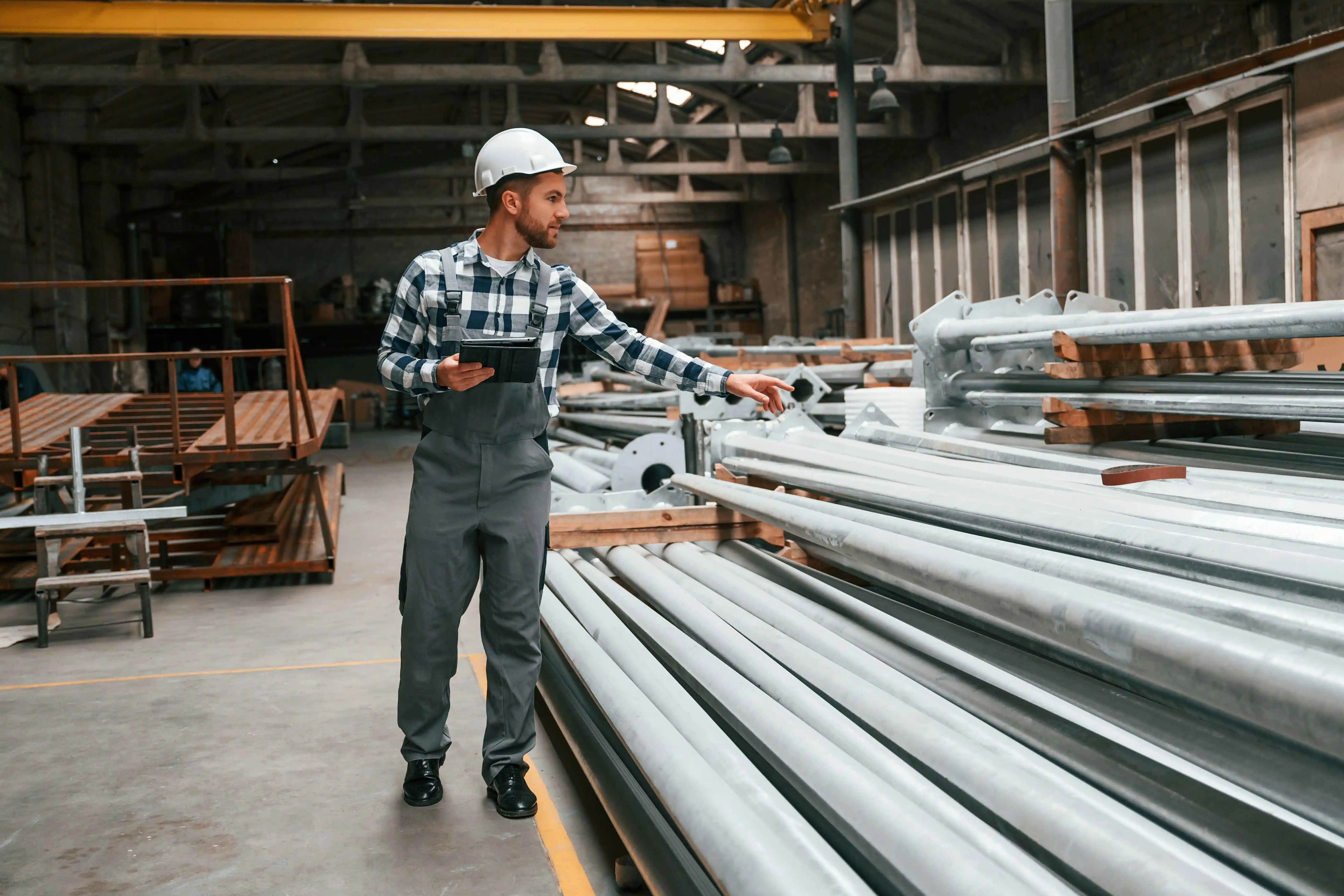
.webp)
together